With the ongoing development of the global economy, there is a consistent upward trajectory in the world’s sea freight container volume, accompanied by a shift towards larger-scale container vessels. Port operators are increasingly prioritizing stable, efficient, energy-saving, environmentally friendly, and cost-effective container loading and unloading processes. The automation and eventual intelligence of container terminal operations emerge as an inevitable trend in the future development of ports. This transition is not only essential for staying in line with industry advancements but is also the sole pathway to achieving high-quality development through the modernization and upgrading of traditional container terminals.
In recent years, there has been a significant surge in the demand for the complete automation of traditional container terminals. The terminal operating system (TOS) utilized by the terminal can currently fulfill the daily production requirements. However, pursuing full automation often involves replacing or upgrading the TOS, potentially impacting production processes. Simultaneously, terminal users seek automated electronic control systems that align with their terminal needs and offer strong cost-effectiveness. Striking the right balance between seamless automation and minimal disruption becomes a crucial consideration for terminals aiming to modernize their operations.
In order to address the above pain points, YM Tech has developed the Smart Solutions Portfolio (SSP). This comprehensive portfolio serves as the central intelligence hub for port equipment automation, bridging the gap between the terminal operating system and the equipment control system. The SSP acts as a cohesive element, enhancing the seamless integration and intelligence of terminal operations.
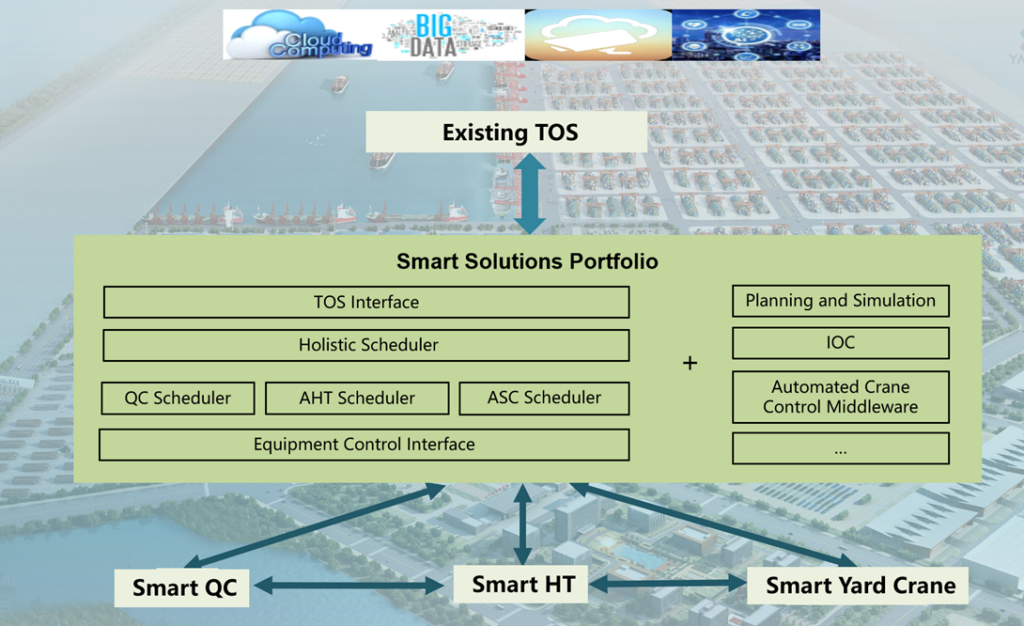
SSP effectively integrates the production, management, and equipment systems of the terminal, establishes information channels between various systems, and achieves automatic issuance of production instructions and analysis and display of production data through automatic collection and sharing of information, achieving the intelligence of the terminal operation process.
SSP eliminates the need for upgrading or replacing the current Terminal Operating System (TOS). Instead, it seamlessly connects with the existing electronic control system of the equipment through middleware. This swift integration process allows for the rapid and efficient automation transformation of the terminal, ensuring a seamless transition without the need for extensive system overhauls.
The overall architecture design of the intelligent integrated control platform for automated terminals is compatible with existing TOS systems and automation equipment, demonstrating excellent scalability to adapt to the rapidly evolving intelligent requirements. The functions of SSP for automated terminals encompass an equipment scheduler system, an intelligent operation center system, and intelligent extension applications.
Container terminal equipment scheduling system is the main part of the intelligent integrated control platform for automated terminals and serves as the equipment scheduling brain for terminal automation. The equipment scheduling system receives work instructions from TOS, assimilates information such as equipment status, location, and command completion from the equipment control system, and autonomously schedules the operations of shore bridges, yard bridges, and horizontal transportation equipment. By facilitating the automatic flow and connection of information in activities such as loading and unloading ships, collection and distribution port operations, and monitoring the execution process of terminal production operations, it optimizes scheduling strategies. This, in turn, reduces the reliance on manual scheduling commands, elevating the automation level of terminal production operations. The resultant improvement in homework efficiency and service quality is a direct outcome of this streamlined and automated approach.
Intelligent operation center (IOC) serves as the intelligent operation and maintenance hub of the terminal. It seamlessly connects data silos through big data platforms, integrating data from various automation systems within the terminal. By leveraging real-time global big data, the IOC generates operational and IT insights. Operational insights include fully automated system bottleneck analysis, single vessel operation efficiency reports, weekly operation reports, and real-time comprehensive large-screen displays, among other functions. Optimization reports provided by the IOC offer objectives and suggestions for optimizing various automation systems, creating a global optimization loop. IT insight extends to the application servers and database servers of all automation systems within the terminal. It proactively pushes sub-health status updates of servers and critical services to the terminal’s IT department and corresponding operation and maintenance suppliers in real-time. Both operational and IT insights proactively communicate efficiency optimizations, terminal operation plan optimizations, IT infrastructure health statuses, and equipment health statuses to terminal users in real-time. This approach achieves proactive operation and maintenance, fostering a more responsive and efficient terminal operation environment.